機械設計をするうえでかならず必要になるのが機器類を収める外装となる「筐体」です。
ここでは筐体の種類や製作工程について解説します。
なお、最近では3Dプリンターを用いて筐体設計を行うことで、製品全体の納期期間や費用面でのコスト削減が見込めます。今後の業務で筐体設計に携わる可能性がある方は、ぜひ最後までご覧ください。
筐体(きょうたい)とは?
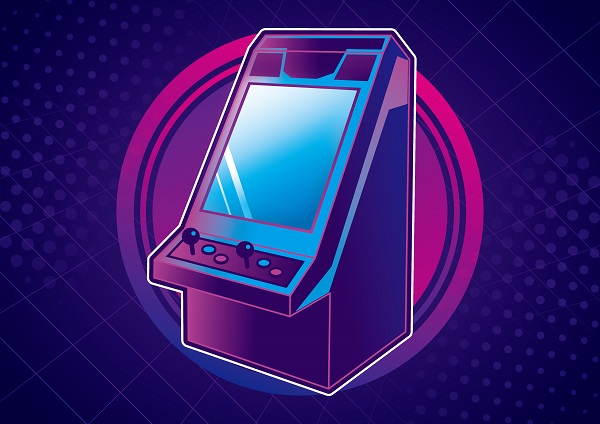
筐体(きょうたい)とは、機器類を収める箱形の容器のことを指します。たとえば、わたしたちが普段使用しているスマートフォンやパソコンなどから、自動車や飛行機などの巨大なものも筐体の一種です。英語では「ケース(Case)」「ハウジング(Housing)」「エンクロージャー(Enclosure)」などとも呼ばれます。
筐体の種類
筐体の種類だけで言えば数え切れないほどになりますが、ここでは代表的な3つを紹介します。
樹脂筐体
樹脂筐体とはプラスチック(合成樹脂)製の筐体です。ABSやPPという樹脂を金型に流し込み、冷やし固める「射出成形」という方法でつくられます。金型次第で複雑な形状の筐体を量産することができ、軽量なのが特徴です。
ダイカスト筐体
ダイカスト筐体とは鉄やステンレスなどの鉄鋼素材や、アルミやチタンなど非鉄金属素材の板を使った筐体です。複雑な形状の筐体を量産する場合に使われ、量産に優れています。
板金筐体
板金筐体とはダイカスト筐体と同様に金属材料の板を使った筐体です。切り出した板材を曲げたり、溶接したりすることで箱のかたちに成形します。
筐体設計の流れとポイント
筐体設計とは機械設計の仕事のうちの1つです。機械設計は動きのない外装をつくる「構造設計」とモーターやギアなど動きのあるものをつくる「機構設計」の2つに分けられます。筐体設計は機械や電子回路などの部品を収納する重要な役割をもつ作業です。内部の機器類が問題なく作動するよう外部から守りつつも、運用面では軽量でなければなりません。
筐体設計は基本的に以下の流れで進みます。
1:構想設計
まず顧客となるターゲット層をどこにするのか、どのように使用するのかを検討します。サイズや重さ、部品の種類、デザインなど製品の基礎となる部分を企画者たちでまとめていきます。
2:基本設計
構想設計で話し合い決めた仕様をもとに具体的な設計図を作成します。実際にどのような部品や材料が必要なのかをCADやCAMなどの図面を作るソフトを用いて検討します。画面上でシミュレーションを行い、今後の工程で問題が発生しないようにしましょう。
3:詳細設計
基本設計で作った設計図をより製造段階で使用できるように調整していきます。設計の精度を高め、加工や組み立ての図面も作成します。製造にかかる金銭的・時間的な面からもコストを洗い出し、強度計算や熱流体シミュレーションなどを行うことも大切です。
4:生産設計
完成した設計図を工場で生産できるように整えていきます。工数が多すぎないか、削減できないかをチェックします。
5:試作品評価
設計した筐体を試作してさまざまな評価を実施します。ときには複数回試作を準備し、つくりに問題がないか検証データをとることも。さまざまな人々からのフィードバックを受け、問題があれば原因を突き止めて対策をします。最終確認が取れたら量産を経て一連の作業が完了です。
筐体の材料
筐体の材料は大きく分けて「金属」と「樹脂」の2種類に分けられます。それぞれメリットが異なるので、求める機能やコストを考えて使い分けることが重要です。
金属
金属のなかでも「鉄鋼」と「非鉄金属」に分けられます。鉄鋼は鋼(スチール)やステンレスなどで、硬くて割れにくいのが特徴です。熱処理によってさらに強度をあげることも。デメリットとしてはサビやすく、重量が大きくなりがちです。安価な素材なのでコスト面でも重宝されます。
非鉄金属はアルミニウムやニッケル、チタンなどです。入手がしやすく、加工性・耐熱性・耐腐食性に優れています。高い強度でありながら軽量なため、筐体としてもっとも用いられている素材です。
樹脂(非金属)
非金属の素材としてよく使われているのが、プラスチック(樹脂)やゴムなどの有機化学物です。金属に比べて強度や耐久性はありませんが、軽くて絶縁性に優れていることが大きなメリットです。加工性も良く、安価に量産が可能です。
そのほか非金属の分類としては、セラミックなどの無機化学物や、金属やプラスチックなど2種類以上の材料を組み合わせた複合材料などが含まれます。
筐体は3Dプリントで楽に安く作れる?
3Dプリンターで作るメリットには以下のようなものがあります。
- 「コスト削減」
- 「リードタイム短縮(すぐに早く造れる)」
- 「素材の種類が豊富」
- 「複雑形状が再現可能」
人件費などのコストを削減できる
3Dプリンターを用いることで、従来の筐体の設計から製造までの効率が大幅に向上します。パソコンの画面上で設計を行い、すぐに出力できることで工場を経由したり人員を確保したりする必要がなくコスト削減が見込めます。
リードタイムの大幅な短縮
なによりも3Dプリンターの良いところは、設計してすぐに出力をして現物を確認できることにあります。手触りや組み立てなど実際に見てみないとわからない箇所の確認時などに重宝されるでしょう。
素材の種類が豊富
プラスチックなどの樹脂に加えて、アクリルや金属製のものも素材として使えるようになってきました。造形可能なサイズや、歪みの問題がありますが今後改善されれば不自由なく使用できます。
複雑な形状が再現可能
切削加工などでは難しい造形物の中に造形物があるような構造など、複雑な形状も3Dプリントであれば無理なく実現できます。組み立て作業も不要にできるので、試作に用いれば作業効率が向上します。
筐体設計・量産に3Dプリンター活用例
『GO Reserve』は行灯やスーパーサインがない車両で運行しているため、一目見て「予約した車だ」と分かりやすくする必要がありました。
そこで車両に搭載するための表示灯の筐体を作っていただきました。
引用:DMM.make 3Dプリント「タクシーの表示灯を40点造形、追加注文も楽に。「3Dプリントは最もコストパフォーマンスが良い製法」GO株式会社 – 活用事例」
筐体を3Dプリンターで作ることでコスト削減に繋がるかも
機器類を収める筐体は3Dプリンターでも作ることが可能です。試作として用いれば、デザイナーやクライアントなどか瞬時にフィードバックをもらうこともでき、大幅な作業の効率化が見込めます。パソコンの画面上で設計ができるので、場所も選ばずに作業が行えるでしょう。
DMM.makeでは3Dプリントの出力代行サービスをおこなっています。ぜひこの機会に筐体の作成をしてみてはいかがでしょうか。